Soldagem por Onda
Existem dois métodos de soldagem de componentes em uma PCI. A Soldagem por Onda ou a Refusão. O que vai definir qual método será utilizado? Os componentes que irão popular a PCI e o lado da PCI que se localizam. Os vários exemplos podem ser vistos no Capítulo referente ao Fluxo de Processo. Iremos nos ater a Soldagem por Onda, pois temos um capítulo específico para Soldagem por Refusão. Vamos lembrar que a soldagem por onda é um modo conveniente de fixar componentes convencionais e componentes SMD colados no lado inferior da PCI. No caso dos componentes convencionais, estes são inseridos através dos furos na PCI e são soldados passando pela onda de solda. O mesmo ocorre com os componentes SMD colados no lado inferior.
A Soldagem por Onda existe a, pelo menos, 50 anos e recebeu uma série extensa de aprimoramentos, mas a essência permanece a mesma. Temos 3 etapas no processo que são:
* Fluxagem; * Pré-Aquecimento; * Soldagem.
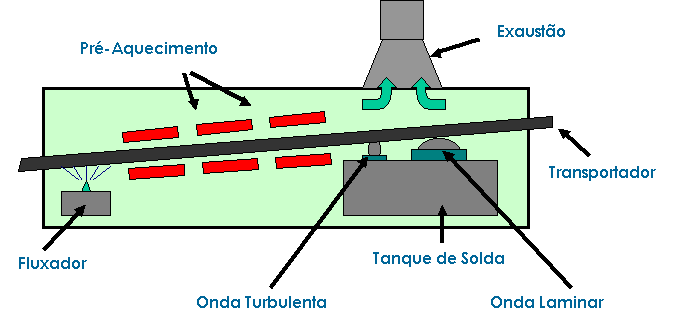
Outras etapas auxiliarem também são consideradas, mas não incluídas no grupo acima. São elas:
Carga de PCI’s na Máquina de Solda Resfriamento da PCI após a soldagem Descarga da PCI
Considerando que o processo de soldagem consiste em etapas individuais, vamos discutir cada uma separadamente.
Camada IntermetálicaAntes de iniciar o detalhamento de cada etapa iremos falar sobre a camada intermetálica. Esta camada é formada entre a junta de solda e a superfície metalizada da PCI. Uma soldagem adequada irá proporcionar uma camada intermetálica mínima. Sua composição Cu6Sn5. Curiosamente o Chumbo (Pb), presente na composição da solda, não está presente na camada intermetálica.
Nota: Saliento que não estamos tratando da nova tecnologia “Lead Free”. Como o próprio nome já diz, na composição química da liga de solda não temos a presença de Chumbo (Pb). As ligas “Lead Free”, com as mais diferentes composições, normalmente apresentam Estanho, Prata e Cobre.
A camada intermetálica, pesar de resistente, se mostra frágil. Quando frágil pode se tornar quebradiça.
Detalhe da Camada Intermetálica Fluxagem Para que uma soldagem possa ser executada, é necessário que as superfícies estejam limpas para que ocorra uma “molhagem” adequada. Tomei o cuidado de colocar o termo “molhagem” entre aspas, pois é de extrema importância. A molhagem resume-se na dispersão da solda sobre uma superfície. Se a solda se espalha pela superfície com facilidade, deduzimos que esta superfície se encontra limpa e isenta de sujeiras e óxidos.
Na soldagem de componentes eletrônicos, a operação de fluxagem faz o trabalho de limpeza e desoxidação da PCI e componentes para que ocorra uma fixação mecânica e elétrica adequada. Ainda melhora a força de capilaridade da solda. Quando se trata de PCI’s com furos metalizados, além de soldar um componente, é necessário que a solda “suba” pelo furo e preencha o espaço entre o terminal do componente convencional. Os métodos de fluxagem serão descritos posteriormente neste capítulo, agora vamos verificar algumas informações conceituais sobre o fluxo propriamente dito. Definição: | “Proporciona três funções principais. A primeira, de remover sujeiras e oxidações. A segunda, aumentar a molhagem e o efeito de capilaridade. A terceira, proteger a superfície durante o processo de pré-aquecimento de uma reoxidação, permitindo uma boa formação da interligação metálica entre as partes”. |
Os componentes encontrados no fluxo são os descritos abaixo:
Solvente: dissolve todos os ingredientes para obtenção de mistura homogênea.
Ativadores: limpam as superfícies a serem soldadas e reduzem a tensão superficial da solda para proporcionar uma boa soldabilidade;
Nota: Cada fabricante detêm e modifica as formulações dependendo da aplicação do produto e suas características técnicas.
Tipos de fluxos existentes
Fluxos com base de resina têm sido utilizados com sucesso e por vários anos na indústria eletro-eletrônica. Suas principais propriedades são:
* Proporcionar remoção da oxidação e efetuar uma suave ação de limpeza nos pontos a serem soldados; * Auxiliar a molhagem (wetting) através da diminuição da força de coesão da solda; * Proteger a superfície durante o aquecimento, de uma reoxidação; * O movimento do fluxo propicia uma melhor dispersão da solda.
Esta escolha está diretamente relacionada com as condições da PCI, componentes e processos estabelecidos. São eles:
Fluxo tipo R:A designação R significa “resinoso”. Seu uso é raro e incomum. É necessária limpeza da PCI após soldagem. Uma de suas raras aplicações é sua utilização nos testes de soldabilidade de componentes; Fluxo tipo RMA: A designação RMA significa “resinoso mediamente ativado”. Tem uso bastante amplo e remove oxidações acentuadas. É recomendada limpeza da PCI após soldagem, mas não obrigatória com nos casos de PCI’s na área de entretenimento; Fluxo tipo NC: A designação NC significa “No Clean”, isto é, não necessita de limpeza após soldagem. Os resíduos sólidos presentes na PCI após soldagem são mínimos. Seu maior inconveniente é sua baixa ativação. A janela de processo é crítica e limitada.O tipo de fluxo tem impacto direto na limpeza das montagens. Nas montagens SMD, devido à pequena distância entre a PCI e os componentes, o fluxo pode ficar retido neste espaço, levando à problemas de confiabilidade, por essa razão os fluxos menos agressivos são preferidos nessas montagens.
Fluxo tipo RA: A designação RA significa “resinoso ativado”. Contém ativadores corrosivos e removem as mais severas oxidações. Necessita uma limpeza criteriosa da PCI após a soldagem. Seu uso é bastante limitado. Fluxo OA ou WS: A designação OA significa “ácido orgânico” ou WS “water soluble (hidrosolúvel)”. Necessita de limpeza da PCI após a soldagem. Esta limpeza ocorre através da lavagem da PCI em equipamento automático, com água deionizada em temperatura próxima a 55º C e o detergente numa concentração que varia entre 1 - 2% para sistema de limpeza semi-aquoso.
Após esta breve descrição sobre o fluxo, vamos tratar da fluxagem propriamente dita.
A seleção do processo específico de soldagem depende de alguns parâmetros:
* O comprimento dos terminais no lado inferior da PCI; * Se a limpeza da PCI é requerida e por qual método; * Condições gerais da PCI a ser soldada; * A quantidade e uniformidade de fluxo requerida; * Segurança e manutenção do equipamento.
Tipos de Fluxadores
Espuma Este método consiste num tanque que pode ser de PVC ou aço inoxidável com uma pedra aeradora, que pode ser natural ou sintética. Através da injeção de ar no interior da pedra aeradora, que por sua vez está submersa no tanque, gera bolhas de ar que se assemelham a espuma, daí o nome. Vale a pena lembrar que alguns fabricantes adicionam aditivos sulfactantes para otimizar a formação da espuma.Para que ocorra efetivamente a fluxagem da PCI, a mesma deverá passar sobre e com em contato com a espuma formada no fluxador.
Este método tem suas vantagens e desvantagens:
Vantagens: * As bolhas que estouram em contato com a PCI otimizam o efeito de capilaridade, pois penetram nos furos por causa do gás presente em seu interior e depositam fluxo nas paredes internas dos furos, melhorando a molhagem e em conseqüência, a soldagem; * É um processo barato, considerando investimento em equipamento.
Desvantagens: * A aplicação não é uniforme; * O tanque normalmente aberto e o fluxo com características higroscópicas, absorve umidade e altera sua viscosidade; * Necessita periodicamente de substituição do fluxo do tanque ou instalação de Controlador de Densidade de Fluxo.
Nota: não se recomenda Controlador de Densidade de Fluxo para fluxos No-Clean.
* Rígido controle da pureza do ar comprimido; * Controle da altura do fluxo, pois se o nível abaixar a ponto de expor a pedra aeradora, a mesma irá apresentar pontos de entupimento. * Controle da temperatura do fluxo, pois também altera a viscosidade.
Spray Em substituição ao tradicional método por espuma, foi desenvolvido o fluxador por aspersão ou spray. Consiste em um tanque de fluxo pressurizado e bicos aspersores. Estes bicos podem ser fixos ou móveis.Quando fixos, normalmente se apresentam em número de 2 ou mais pela necessidade de aplicar fluxo em PCI’s largas. Quando móveis, apresentam um único bico que percorre a PCI no sentido transversal aplicando uma camada uniforme de fluxo. Vantagens: * Aplicação uniforme de fluxo; * Economia; * Estabilidade da densidade; * O não depósito de fluxo entre os componentes SMD e a PCI.
Desvantagens: * Investimento inicial; * Limitação de aplicação de fluxos com alta porcentagem de sólidos; * Menor capilaridade que o fluxador por espuma.
Ultrasônico
O Fluxador Ultrasônico tem o mesmo príncipio do fluxador por aspersão ou spray com uma peculiaridade: possui um transdutor ultrasônico que “quebra” as partículas de fluxo, transformando-as em uma névoa, tanto que esta operação se caracteriza como nebulização.
Vantagens: *Aplicação de fluxo seletiva e com alta precisão; * Economia; * Estabilidade da densidade; * O não depósito de fluxo entre os componentes SMD e a PCI.
Desvantagens: * Investimento inicial; * Limitação de aplicação de fluxos com alta porcentagem de sólidos; * Menor capilaridade que o fluxador por espuma.
Pré-Aquecimento Esta etapa do processo tem as seguintes funções básicas: * Aquecer a PCI com o objetivo de reduzir o stress térmico durante sua passagem pela Máquina de Solda por Onda; * Evaporar os solventes presentes no fluxo; * Minimizar a diferença de temperatura (Delta T) na PCI; * Ativar os fluxos resinosos. Tanto o fluxo No-Clean como os orgânicos têm sua ativação na temperatura ambiente mas se tornar mais ativos durante o processo de pré-aquecimento da PCI; * Promover a subida da solda pelo furo (em componentes de tecnologia convencional) e seu respectivo preenchimento com solda.
Tipos de Pré-Aquecimentos Existem dois métodos de transferência de calor comumente utilizados. São eles: o infra-vermelho e convecção forçada dominante.
1. Infravermelho Em sistemas infravermelhos dedicados, lâmpadas ou elementos de resistência são utilizados para gerar energia (photons) em comprimentos de onda infravermelha. Esta energia produz calor que é absorvida pelo produto.
Pré-Aquecimento Infra-Vermelho
Apesar do infravermelho significar uma eficiente forma de transferência de calor, problemas se potencializam quando utilizamos apenas o infravermelho para soldagem por onda. A transferência de calor por infravermelho depende diretamente do comprimento de sua onda e da cor e massa dos corpos presentes durante a soldagem, que são seletivamente absorvidos. A emissividade (a cor determina a característica do material) varia numa faixa que vai de “zero” até “um” onde os objetos mais brilhantes tem classificação menor e os objetos escuros ou negros próximos de “um”. Emissividade maior significa maior absorção de calor. Corpos escuros ou negros absorvem calor enquanto objetos claros ou brilhantes refletem esta energia.O problema com isto é que os objetos com maior emissividade na PCI não são necessariamente os objetos que precisam de maior aquecimento. Isto é especialmente verdade,pois os encapsulamentos são tipicamente escuros (alta emissividade), e as uniões de solda são brilhantes e tem baixa emissividade. Como resultado, componentes com encapsulamentos negros se aquecem mais rapidamente que as uniões de solda e outros componentes de cores diferentes. Este efeito provoca um aumento significativo nos diferenciais de temperatura em pontos distintos da PCI quando utilizamos como energia por processo infravermelho.Outro agravante é o efeito sombra. Algumas áreas na PCI não são atingidas pelas ondas do infravermelho, comprometendo ainda mais a uniformidade da temperatura em diferentes pontos da PCI. Problemas de controle também são inerentes dos sistemas infravermelhos dedicados. Os emissores de calor devem ser ajustados em excesso para se obter a temperatura desejada resultando na dificuldade de se determinar a temperatura requerida e consequentemente, o perfil de temperatura desejado. Adicionalmente, grandes flutuações de temperatura ocorrem baseadas na carga de produção. Apesar de todas estas objeções, este é um método ainda utilizado por algumas empresas onde os requerimentos processuais não são rígidos ou os lotes de produção são limitados.
2. Convecção forçada dominanteSistemas de Convecção forçada dominante não são emissivos como os infravermelhos. A uniformidade do calor através da superfície da PCI é constante e o efeito sombra não ocorre, pois o efeito de capilaridade do fluxo laminar de ar atinge todos os pontos da PCI. O controle de sistemas por Convecção é mais preciso. A temperatura do fluxo de ar que atinge a PCI é muito próxima à temperatura desejada no produto. O controle deste sistema é realizado rapidamente monitorando a temperatura do fluxo de ar através de termopares que estão instalados em posições específicas e definidas. A consistência de processo é maior proporcionado menos defeitos e resultando um resultado satisfatório.
Em Máquinas de Solda por Onda podemos ter seções de pré-aquecimento tanto na parte inferior do equipamento como na parte superior. Isto vai depender dos requerimentos de processo e deve ser observado o material do substrato da PCI, o número de camadas da PCI (no caso de PCI’s Multicamadas), a população de componentes, tanto na face inferior da PCI como na face superior entre outros fatores. Pré-Aquecimento por Convecção
Transportadores de PCI’s A PCI deve ser transportada através das seções de Fluxagem, Pré-Aquecimento e Soldagem através de Pallets ou garras, comumente chamadas de “fingers” (dedo, em inglês).
É necessário que a PCI esteja bem fixa e nivelada, pois qualquer alteração na distância entre a face inferior da PCI e a onda de solda poderá provocar problemas de soldagem ou mesmo acidentes, pois a solda poderá “passar” sobre a face superior da PCI e inutiliza-la. Os dois tipos mais utilizados são os Tipo L e Tipo V como segue:
Tipo L
Adequado para receber PCI’s de grandes dimensões. Alguns fabricantes especificam PCI’s até 11 Kgs. O próprio peso da PCI impede que a mesma se mova durante a passagem pela Máquina de Solda por Onda.
Tipo V É o mais popular e utilizado. O termo “finger”se deve ao formato desta garra metálica, normalmente de Titânio para que não haja contaminação da solda já que entra em contato com a solda no momento da soldagem da PCI. Fixa a PCI através do efeito mola que a garra proporciona.
Velocidade do Transportador A velocidade do transportador é de fundamental importância para o processo de soldagem. Ela vai definir a camada de fluxo aplicada, o pré-aquecimento da PCI e o tempo que a PCI irá estar em contato com a onda de solda. Pode haver a necessidade de maior período de contato entre a PCI e a onda de solda nas seguintes condições: * Espessura da PCI; * PCI’s multicamadas; * Planos Terra densos dentro da PCI; * Soldagem Convencional (PCI’s com furos metalizados); * Tipo/nível de ativação dos fluxos utilizados.
Normalmente a velocidade do transportador varia entre 1,0 e 1,5 metros/minuto. A definição da velocidade vai depender de vários fatores (além dos mencionados imediatamente acima). O Perfil Térmico é determinante para uma boa qualidade final de soldagem.
Perfil Térmico Apenas relembrando o que já foi mencionado na seção onde descrevemos o processo de refusão com o uso de pasta de solda. O que determina a curva de temperatura é a pasta de solda. No caso da soldagem por onda devemos levar em consideração os seguintes itens:
Temperatura na face superior da PCI. O motivo principal é a integridade térmica de componentes sensíveis a altas temperaturas. Outro fator importante é a ativação do fluxo que se aloja nos furos e permite que a solda “suba” e preencha adequadamente o furo metalizado; Temperatura dos componentes na face inferior da PCI; Taxa de aquecimento. Quão rápido a PCI e componentes estão aquecendo. Fabricantes de componentes recomendam um aquecimento entre 2 e 3 C°/seg. O Perfil Térmico normalmente é levantado com o auxílio de um simples equipamento coletor da temperatura.Em curtíssimos espaços de tempo, estes números são coletados e armazenados em um Circuito Integrado, que posteriormente descarrega todos os dados coletados num programa que acompanha o coletor. Nada impede que você tente ajustar o Perfil Térmico na “raça”. Com certeza, será mais complicado e demorado. A coleta é feita com o auxílio de termopares ligados em diferentes pontos na PCI e ao coletor. Esta ligação é física (através de cabos). Para informações adicionais, o leitor poderá acessar o site http://www.ecd.com/. Esta empresa fabrica a marca SuperMole®. A figura abaixo mostra como é a tela do software com os dados coletados. O coletor fornece várias informações tais como: * Velocidade do transportador; * Temperatura(s) em cada zona; * Temperaturas máximas e mínimas; * Deltas de temperaturas; * Tempo da PCI nas diversas etapas de soldagem; * Entre outras.
Tanque de Solda
Após as operações de Fluxagem (onde a PCI recebeu o fluxo que retirou as sujeiras (óleos, graxas, etc.) e as oxidações) e Pré-Aquecimento (onde a PCI e componentes receberam uma carga térmica consiste e dentro de limites que mantiveram sua integridade, e ainda, onde os componentes do fluxo foram devidamente ativados e o solvente volatilizado), a PCI finalmente vai para a etapa final do processo de soldagem: a Onda de Solda. A onda de solda é formada por bocais instalados dentro do tanque de solda. A configuração destes bocais vai depender do tipo de PCI que será soldada. Caso o Cliente tenha uma PCI, apenas com componentes convencionais, então uma onda laminar (ou “lambda”) será suficiente para que a solda derretida entre em contato com os terminais e efetue a soldagem. Iremos tratar de cada bocal em separado mais adiante. Acabei de mencionar “que a solda derretida...”. Para que possamos seguir em frente precisamos parar um pouquinho e falar da solda que vai dentro do tanque. Solda Normalmente fornecido em lingotes dispostos em caixas de 25 Kg. A quantidade de solda vai depender das dimensões do tanque de solda. Estas dimensões dependem de vários fatores, tais como; * Volume de produção; * Largura do tanque de solda; * Estabilidade térmica; * Tipos de Bocais utilizados; * Etc.
Durante a configuração de uma máquina de solda é muito importante que se defina a necessidade atual e futura. Às vezes, a adição de um bocal,não é possível por limitações no tanque de solda. Esta quantidade pode variar de 200 kg até 1000 Kg! A solda normalmente é composta de Estanho (Sn) e Chumbo (Pb) em porcentagens de 63% e 37%, respectivamente. Algumas aplicações requerem o uso de Prata (Ag) em baixas porcentagens (2%). Caso tentássemos fundir apenas Estanho (Sn), a temperatura de fusão seria de 232 °C (450oF). Caso tentássemos fundir apenas Chumbo (Pb), a temperatura de fusão seria de 327 °C (621oF). Nesta porcentagem de Sn 63% e Pb 37%, os metais se tornam uma liga eutética e se fundem simultaneamente à 183oC (361oF). A adição de Prata (Ag) modifica a liga para Sn 62% Pb 36% e Ag 2%. A seguir iremos descrever a razão da adição da Prata.
A Prata: * diminui o ponto de fusão para 179oC (354oF); * torna a solda mais brilhante; * melhora as características mecânicas; * é compatível com os terminais banhados com liga Sn 62% Pb 36% e Ag 2%.
Falamos anteriormente que o ponto eutético da liga Sn 63% e Pb 37% é de 183oC (361oF) e que, com o uso da Prata cai para 179oC (354oF). A pergunta pode ser: qual é a vantagem? Os tanques de solda são ajustados paramanter uma temperatura da solda em 250oC (482oF). Caso se tenha uma liga que pode abaixar um pouco esta temperatura, ela é totalmente desejável. O fato de tornar a solda brilhante é uma questão de especificação de inspeção. Alguns usuários dizem que a solda brilhante é melhor de se inspecionar. Outros usuários especificam o uso de pequenas porcentagens de Bismuto (Bi) para tornar a solda com acabamento opaco. Mas cuidado, o Bismuto fragiliza a solda.Fato que a Prata age de maneira oposta, aumentando a resistência da solda. Vou explicar melhor o item referente aos terminais banhados com 2% de Prata. O que ocorre é um problema de ordem estética, mas que deve ser mencionado. Atualmente alguns fabricantes de componentes estão banhando os terminais dos componentes com a liga com 2% de Prata. Caso o usuário solde estes componentes, tanto em processo por soldagem a onda como por refusão, com uma liga eutética, vai ocorrer o que chamamos de “migração da Prata”. A Prata (da liga Sn 62% Pb 36% e Ag 2%) migra para a liga eutética, causando manchas que, apesar de totalmente estéticas, são indesejáveis. Usando sempre barras ou pasta com 2% de Prata, esta ocorrência é evitada.O ponto a ser considerado é que, por se tratar de Prata, tanto a barra de solda como a pasta de solda tem preços diferenciados. Bocais de SoldagemOs Bocais de Soldagem geram diferentes tipos de onda no tanque de solda. Cada onda tem uma função e sua especificação depende da aplicação. Soldagem de componentes de tecnologia convencional e/ou componentes SMD posicionados na face inferior da PCI necessitam de soldagem por onda. Para maiores detalhes consultar o Capítulo III – Fluxos de Processo – e verificar os Tipos II, III e V. O uso de mais de uma onda é comum. Tanto em ambiente a ar como inerte, pode-se usar o método de soldagem por onda, apenas respeitando o perfil de cada onda, pois em ambiente inerte os bocais têm um desenho diferente dos bocais que utilizamos em ambiente a ar. O assunto do ambiente inerte terá um capítulo específico.
Bocal para Onda Laminar (Lambda)
Utilizado na soldagem de componentes de tecnologia convencional. Esta onda se caracteriza pelo aspecto liso e fluxo suave.
O princípio da Onda Laminar está demonstrado abaixo. Como podemos notar na figura acima, existe uma área estacionária. A solda bombeada de forma ascendente flui pela seção frontal do bocal. Assim que a PCI entra em contato com a onda laminar as velocidades V1 e V2 se igualam, gerando uma condição ideal de saída da PCI.
Bocal para Onda Turbulenta
Quando se necessita soldar componentes de tecnologia convencional eSMD na face inferior da PCI, o uso da onda turbulenta é mandatório. A onda turbulenta é formada por um bocal instalado na parte frontal do tanque (consideramos o sentido do transportador para definir a frente e traseira do tanque de solda).
Posicionado antes do bocal para onda laminar e com uma inclinação de aproximadamente 15° em relação ao transportador, efetua a molhagem dos componentes SMD eliminando o efeito “sombra”. O efeito “sombra” se define pela área (face traseira) do componente que não entra em contato com a onda de solda laminar e, por conseguinte não recebe quantidade suficiente de solda.
Cerca de 60% do fluxo remanescente é lavado da PCI na onda turbulenta. É necessário que haja uma outra parte residual de fluxo durante a passagem da PCI na onda laminar para que a tensão superficial da onda seja reduzida e uma boa junção intermetálica seja formada.
O controle da altura da onda turbulenta é muito importante para que a quantidade de solda seja suficiente para formar uma boa junção intermetálica. Se tivermos uma onda de solda com altura insuficiente, o efeito “sombra” não será eliminado e, uma altura excessiva causará uma inundação da PCI. A solda passará sobre a PCI e a mesma estará condenada para uso.
Soldagem em Ambiente Inerte (Nitrogênio)
Muito já se falou sobre o uso de gases inertes durante o processo de soldagem, seja por onda como por refusão. O gás inerte mais popular é o nitrogênio. Além de participar com 79% da composição de nosso ar, é um gás nobre. A razão efetiva de seu uso é, essencialmente, devido a sua abundância em nossa atmosfera. Sua injeção através de difusores nas ondas de solda (turbulenta e laminar), afastam e neutralizam a ação do oxigênio e sua respectiva oxidação durante o processo de soldagem.
O uso de nitrogênio proporciona:
* Uniões de solda brilhantes. Isso não significa que sejam mais resistentes; * Reduz a formação de óxidos (borra) e com isso, menos solda é usada, menos borra é formada e, conseqüentemente se faz uma menor interferência para manutenção no tanque de solda. Isto não significa que não haja manutenção, pois uma série de acessórios são instalados para que o uso do nitrogênio possa ser viabilizado; * Menor oxidação das superfícies metalizadas; * Aumenta a janela de processo para fluxos menos agressivos; * Elimina um defeito denominado pingente (veja abaixo)
Algumas combinações são totalmente indesejáveis. Uma delas é o uso de fluxos com alta porcentagem de sólidos em ambiente inerte. O nitrogênio reduz significativamente a tensão superficial na onda de solda e o fluxo com alta porcentagem de sólidos potencializa esta redução da tensão superficial, possibilitando o aumento da formação de curtos. O uso de nitrogênio possibilita o aumento de bolas de solda (solder balls). O tipo de máscara de solda utilizada também influência na formação de bolas de solda.
Ondas Turbulenta e Laminar em ambiente inerte Diretrizes de Soldagem por Onda * Sempre que possível e/ou disponível, utilize a onda turbulenta; * Otimizar a orientação dos componentes e projeto das ilhas; * Checar se componentes grandes não estão fazendo “sombra” nos componentes menores; * Verificar se o projeto da PCI contempla o uso de ladrões de solda nos circuitos integrados; * Assegurar que a rampa de aquecimento dos componentes não exceda as especificações técnicas dos fabricantes; * Manter a diferença de temperatura entre a solda e os componentes cerâmicos abaixo de120oC prevenindo assim, choques térmicos; * Observar a largura da PCI e sua flexão durante a soldagem, evitando assim, alagamentos na PCI;* Em casos onde se utilizam componentes convencionais, atentar-se ao comprimento dos terminais; * Verificar a relação entre diâmetro ou área do terminal em relação ao furo onde o mesmo está inserido; * Velocidade da PCI no transportador. Lembrar que fluxos “No-Clean” necessitam de exposição no pré-aquecimento por, pelo menos, 1 minuto; * Qualidade da máscara de solda. Tanto máscaras de solda muito espessas, bem como máscara de solda muito lisa, pode aumentar a incidência de falhas na soldagem; * Solda contaminada ou fluxo com densidade alterada favorecem a não molhagem nos furos da PCI; * Transportador com movimento suave e velocidade constante. A granulação da solda pode se dar devido a vibrações na esteira de transporte.
Existem 3 categorias principais de Defeitos. São elas:
1. Relativa aos Materiais * Contaminação da solda; * Fluxo sujo ou contaminado; * Máscara de solda.
2. Relativa a Soldabilidade * Contaminação da PCI; * Problemas de fabricação nos furos metalizados da PCI (PTH); * Contaminação dos terminais dos componentes.
3. Relativa ao Processo * Aplicação de fluxo – falta ou excesso, inconstante; * Temperaturas de pré-aquecimento e perfis de temperatura incorretos; * Velocidade do transportador muito rápido ou devagar; * Temperatura da solda muito alta ou baixa; * Fluxos de nitrogênio incorretos; * Ajuste indevido dos bocais; * Excesso de óxidos (borra) no tanque de solda.
10 Principais Variáveis que influenciam a Solderabilidade
1. Solderabilidade das PCI (ilhas/furos) e componentes. 2. Seleção do Fluxo – habilidade do fluxo de remover as oxidações. 3. Aptidão do Fluxador por Spray * Penetração do fluxo nos furos metalizados da PCI; * Uniformidade na deposição do fluxo; * Consistência na aplicação do fluxo. 4. Temperatura do pré-aquecimento e perfil térmico 5. Uso de nitrogênio. Taxas de aplicação corretas 6. Temperatura da solda 7. Tempo de contato entre a PCI e a onda de solda (dwell time) * Controlado através da velocidade do transportador 8. Ajuste da Onda de Solda * Profundidade da Onda * Taxa de saída/queda da onda laminar 9. Condições Gerais dos terminais do componente 10. Orientação e lay-out do componente e geometria das ilhas na PCI.
|